1. Introduction to Polca
Definition of Polca
Polca, an acronym for “Paired-cell Overlapping Loops of Cards with Authorization,” is a visual, card-based production control system designed to manage workflow on the shop floor. It is particularly suited for high-mix, low-volume, and custom-engineered manufacturing environments. By controlling the movement of jobs between workstations,
Origin and History
Developed in the late 1990s by Rajan Suri, Polca emerged as a component of Quick Response Manufacturing (QRM), a strategy aimed at reducing lead times across manufacturing operations. Recognizing the limitations of traditional systems like Kanban in custom and low-volume production settings, Suri introduced Polca to address the unique challenges faced by such industries.
Importance and Relevance
In today’s manufacturing landscape, characterized by increasing demand for customized products and shorter lead times, Polca offers a robust solution. Its design caters to environments where variability and customization are prevalent, ensuring efficient workflow management and enhanced responsiveness to customer needs. By implementing Polca, companies can achieve significant improvements in delivery performance and operational efficiency.
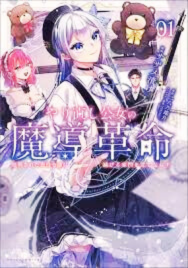
2. Understanding Polca
Key Characteristics
Polca distinguishes itself through several key features:
- Card-Based System: Utilizes physical or digital cards to signal authorization for job movement between workstations.
- Paired-Cell Structure: Establishes overlapping loops between pairs of work cells, facilitating controlled workflow.
- Capacity Signaling: Ensures that a workstation only begins a new task when downstream capacity is available, preventing bottlenecks.
How Polca Works
In a Polca system, each pair of workstations shares a set of cards. A job can only move from one workstation to the next if a Polca card is available, indicating that the downstream workstation is ready to receive and process the job. This mechanism controls WIP levels and maintains a balanced workflow across the production floor.
Applications and Usage
Polca is particularly effective in industries where products are custom-made or produced in low volumes. It has been successfully implemented in sectors such as machinery manufacturing, aerospace, and specialized equipment production. Companies facing challenges with traditional push or pull systems find Polca advantageous due to its adaptability to high variability in production processes.
3. Benefits of Polca
Advantages Over Other Systems/Methods
Compared to traditional systems like Kanban, which are optimized for high-volume, repetitive manufacturing, Polca offers distinct advantages:
- Flexibility: Adapts to varying product types and production volumes.
- Reduced Lead Times: Minimizes delays by ensuring workstations are only tasked when capacity is available.
- Lower WIP Levels: Controls inventory buildup, leading to cost savings and improved space utilization.
Efficiency and Effectiveness
Implementing Polca leads to streamlined operations, as it prevents overproduction and ensures resources are optimally utilized. By maintaining a balanced workflow, manufacturers can respond more swiftly to customer orders, enhancing satisfaction and competitiveness.
Industries That Benefit from Polca
Industries characterized by custom orders and low-volume production, such as aerospace, specialized machinery, and custom fabrication, have reported significant improvements in operational metrics after adopting Polca. These include reductions in lead times, improved on-time delivery rates, and decreased inventory levels.
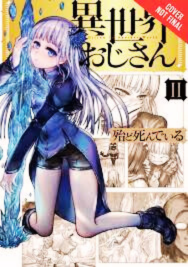
4. Implementation of Polca
Steps to Adopt Polca
- Assess Production Environment: Determine if your operations involve high variability and customization.
- Design Workflow Cells: Organize workstations into cells that handle specific tasks or product families.
- Establish Card Loops: Define overlapping card loops between paired cells to control job movement.
- Train Personnel: Educate staff on Polca principles and procedures to ensure smooth adoption.
- Monitor and Adjust: Continuously evaluate the system’s performance and make necessary adjustments.
Best Practices
- Start Small: Pilot Polca in a single department before a full-scale rollout.
- Engage Employees: Involve shop floor workers in the design and implementation process to gain valuable insights and foster ownership.
- Leverage Technology: Consider digital Polca solutions to enhance real-time tracking and reduce manual errors. axxalon.com
Common Challenges and Solutions
- Resistance to Change: Overcome this by demonstrating Polca’s benefits through training and pilot programs.
- Complex Production Flows: Simplify processes where possible and ensure clear communication channels between cells.
- Card Management: Utilize digital tools to track cards and job statuses, reducing the risk of lost or misplaced cards. axxalon.com
5. Comparing Polca with Other Methods
Differences Between Polca and Similar Approaches
While both Polca and Kanban are card-based systems, Kanban relies on inventory levels to trigger production, making it suitable for repetitive manufacturing. In contrast, Polca uses capacity signals, ensuring that workstations only take on new jobs when downstream capacity is available, which is ideal for high-mix, low-volume environments.